Mastering Laser Cutting Design: A Step-by-Step Guide for Precision and Creativity
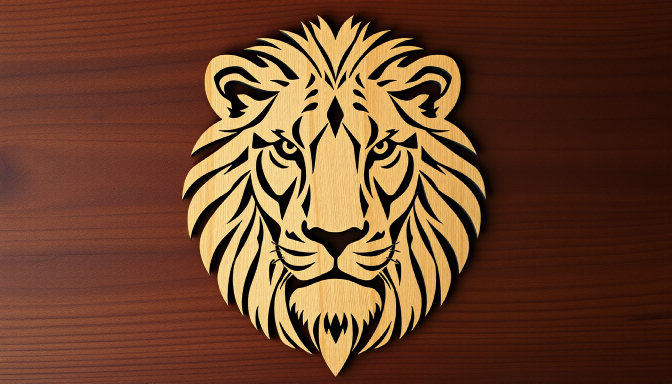
In this guide, “Mastering Laser Cutting Design: A Step-by-Step Guide for Precision and Creativity,” we’ll walk you through the essential steps to create accurate and effective designs for laser cutting technology. As laser cutting grows in popularity for its ability to produce intricate patterns on materials like wood, acrylic, and metal, understanding the design process is key to achieving professional, polished results.
From selecting the right software and crafting precise vector designs to fine-tuning your settings and optimizing for efficiency, this guide equips you with the tools to bring your creative ideas to life. Whether you’re just starting out or looking to refine your skills, this resource will help you navigate the process and create designs that combine precision, functionality, and flair.
Understand Laser Cutting Basics
Familiarize Yourself with How Laser Cutting Works
Understand that a laser cutting machine uses focused laser beams to melt, burn, or vaporize materials. Recognize the common types of lasers used in cutting:
- CO2 lasers: Ideal for non-metal materials like wood, acrylic, and plastics.
- Fiber lasers: Best for cutting metals such as steel, aluminum, and copper.
- Diode lasers: Effective for non-metals, thin metals, and fine detail work. They are compact, efficient, and ideal for smaller projects.
Explore the Various Materials You Can Cut with a Laser
- Wood: Produces clean cuts and allows for intricate designs.
- Acrylic: Offers vibrant colors, smooth edges, and fine detail in cutting and engraving.
- Metals: Requires a fiber laser or specialized diode laser for effective cutting and engraving.
- Fabrics: Ideal for creating patterns and designs without fraying or unraveling.
Assess the Capabilities and Limitations of Your Laser Cutting Machine
- Material Thickness: Review the maximum material thickness your machine can cut effectively.
- Speed and Power Settings: Check the available speed and power options for precision and efficiency.
- Precision Level: Understand how well your machine handles fine, intricate designs.
- Cooling and Maintenance: Consider the cooling system requirements and regular maintenance needed for optimal performance.
Gather Knowledge for Success
Having a solid understanding of your laser cutting machine’s strengths and limitations ensures you can make the most of your projects. From choosing the right materials to adjusting settings, this knowledge will help you produce clean, professional results every time.
Choose Your Design Software
Choose the Right Software for Laser Cutting
LightBurn is a powerful and user-friendly software specifically designed for laser cutting and engraving. Unlike general vector design tools, LightBurn allows you to design, arrange, and optimize your projects all in one place. With its intuitive interface, you can create vector graphics, edit shapes, and adjust laser settings such as power, speed, and passes directly within the software. Compared to Adobe Illustrator or CorelDRAW, LightBurn eliminates the need to switch between design and laser control software, making it a preferred choice for laser enthusiasts seeking an all-in-one solution.
Choose software that specializes in vector graphics, as this is essential for precise designs suitable for laser cutting. Adobe Illustrator is a leading choice, offering extensive tools for creating intricate vector artwork. Familiarize yourself with its interface and features, like the Pen tool and Shape Builder, which will help you craft detailed designs. If you prefer a more budget-friendly option, consider CorelDRAW; it’s user-friendly and supports a variety of file formats.
Explore Inkscape if you want a free, open-source alternative. It includes many powerful features found in paid software and allows you to create and edit vector graphics effortlessly. When selecting your software, ensure it can export files in formats like SVG, DXF, or AI, as these are compatible with most laser cutters. Check the software’s documentation or help section for guidance on exporting files correctly.
Create a Vector Design
Open your chosen vector design software, such as Adobe Illustrator, Inkscape, CorelDRAW, or LightBurn. Start by creating a new document and set the dimensions to match the exact size of the material you plan to use for your project. Accurate dimensions ensure your design will fit the material perfectly and avoid costly errors.
Use Vector Graphics for Precision
Vector graphics are essential for laser cutting because they are composed of paths defined by mathematical equations. These paths allow the laser cutter to follow precise lines, ensuring clean and accurate cuts. Avoid using raster images (bitmap graphics) as they rely on pixels and are unsuitable for cutting applications. If you’re working with a design that contains raster images, convert those elements to vector paths using tools like Illustrator’s Image Trace or Inkscape’s Trace Bitmap feature.
Set Line Thickness and Stroke for Cutting
Adjust the line thickness (stroke width) to meet the specifications required for your laser cutter. A stroke width of 0.001 inches (0.025 mm) is typically ideal for cutting applications. This thin line indicates to the laser software that the path is for cutting rather than engraving or scoring. For elements requiring engraving, use thicker strokes or filled areas to differentiate them.
Pay Attention to Scaling and Proportions
Precision is key when working with laser cutting projects.
- Match Dimensions: Measure your material carefully and ensure your design adheres to these exact measurements.
- Proportional Scaling: Keep all elements proportional as you resize or adjust shapes. For example, if you’re designing a wooden coaster set, ensure that each coaster’s diameter fits neatly within the material size.
To avoid alignment or fitting issues, add a slight clearance (kerf adjustment) around elements that need to slot or fit together, like puzzle pieces or interlocking parts.
Preview and Optimize Your Design
Before sending your file to the laser cutter:
- Preview the Design: Use your software’s preview feature to check for overlapping paths, incomplete shapes, or unintended gaps.
- Make Adjustments: Ensure all vector lines are clean, connected, and free of stray points. Misaligned paths or artifacts can result in incorrect cutting.
- Save in the Right Format: Export your design in a compatible file format such as SVG, DXF, or AI, depending on your laser cutter’s requirements. Double-check software settings for precision.
By following these steps, you can ensure your design is optimized for laser cutting, resulting in clean, precise cuts and professional-quality projects. Whether you’re crafting intricate designs for wooden coasters, acrylic art pieces, or interlocking components, attention to detail in the design phase will set your project up for success.
Set Up Your File for Laser Cutting
Organize Your Design for Laser Cutting and Engraving
Group elements in your design based on their function—cutting or engraving. Assign distinct colors to differentiate between operations; for example, red for cuts and blue for engravings. This helps the laser software recognize which areas to cut and which to engrave.
Ensure all paths are closed for cutting lines. Open paths can cause incomplete cuts or misinterpretation by the laser cutter. Use tools like Pathfinder in Adobe Illustrator or Combine in Inkscape to merge or fix any open paths. Zoom in on key intersections to verify everything is properly connected.
Check that your design fits within the laser cutter’s workspace. Measure the dimensions of your design and compare them with your machine’s specifications. If needed, rescale or reposition elements to stay within the boundaries. For larger projects, divide the design into smaller sections that can be cut individually and assembled later.
By organizing layers and confirming all paths and dimensions, you’ll ensure a smooth, accurate cutting and engraving process.
Select Material and Settings
Choose the Right Material for Your Project
Selecting the appropriate material is critical to achieving the desired finish, functionality, and precision in your laser cutting projects. Start by evaluating your design needs:
- For lightweight prototypes or decorative pieces, materials like cardstock, thin plywood, or acrylic work well.
- For sturdier projects requiring durability, consider thicker plywood, hardwoods, or metals.
Be sure to check your laser cutter’s compatibility with the material. Some machines handle specific materials better than others, such as CO₂ lasers excelling with wood and acrylic, while fiber lasers are ideal for metals.
Optimize Cutting Settings for Your Material
Refer to your laser cutter’s manual or manufacturer guidelines to identify the recommended settings for your chosen material. Focus on key parameters such as:
- Power: Determines the strength of the laser beam.
- Speed: Controls how quickly the laser moves across the material.
- Frequency (or PPI): Adjusts the pulse rate of the laser for clean and accurate cuts.
Perform trial cuts to fine-tune these settings, testing slight variations to avoid burning, charring, or warping. Keep notes of successful combinations of power, speed, and frequency for each material type and thickness. Maintaining a cutting log will save time on future projects and ensure consistent results.
Choosing the right material and optimizing settings not only improves the quality of your work but also enhances efficiency, helping you achieve clean, professional cuts every time.
Test Your Laser Cutting Design
Perform a Test Cut for Precision
Before starting your final project, run a test cut using scrap material that matches the thickness and type of your final piece. This allows you to verify your settings and identify any potential issues before committing to the actual material.
Load your design into the laser cutter and set the parameters based on the material specifications, including power, speed, and depth. Start the cutting process and observe carefully for problems such as misalignment, inconsistent depth, or excessive burning.
After the test cut, evaluate the results closely:
- Inspect the edges for smoothness and precision.
- Check the contours for clarity and completeness.
- Look for signs of charring, overburn, or incomplete cuts.
If imperfections are present, adjust your settings accordingly. Tweak the speed, power, or focus height to correct any issues. Make small, incremental changes and rerun the test cut until you achieve clean, accurate results.
By fine-tuning your settings through test cuts, you ensure that your final project will be executed flawlessly, saving material and time while delivering a professional finish.
Final Cut and Assembly
Finalize and Assemble Your Project
Begin by carefully reviewing the test cut results to ensure every detail meets your expectations. Once satisfied, set up your laser cutting machine for the final run. Double-check that the material is securely placed and that all settings—such as power, speed, and focus—are accurately calibrated for precision. Monitor the cutting process closely to identify and address any potential issues, like misalignment or incomplete cuts, before they affect the final outcome.
After the pieces are successfully cut, organize the components methodically according to your design layout. This step ensures a smooth and efficient assembly process. Use appropriate adhesives, fasteners, or joinery techniques as required by your project specifications to connect the pieces securely.
Pay attention to any finishing touches that enhance the overall quality of the final product:
- Sanding: Smooth out rough edges for a clean, professional look.
- Painting or Staining: Add color or protection based on the project’s aesthetic requirements.
- Sealing: Apply finishes like clear coats or varnish to protect the material and achieve a polished appearance.
Take your time during assembly to ensure each piece fits together seamlessly. Attention to detail at this stage will ensure that the final product is sturdy, visually appealing, and meets your original design vision.
Key Takeaways to Master Laser Cutting Design
Bringing It All Together
Mastering laser cutting design involves understanding the process, selecting the right software, creating precise vector designs, and rigorously testing your settings. By carefully following each step, you can transform your ideas into reality with accuracy and creativity. With the right approach, your laser-cut projects will showcase both precision and craftsmanship.
Take your time, embrace the learning process, and let your creativity shine. Happy designing! Check out our projects page and follow us on YouTube for more!