Laser Power 101: More Wattage or Smarter Choices?
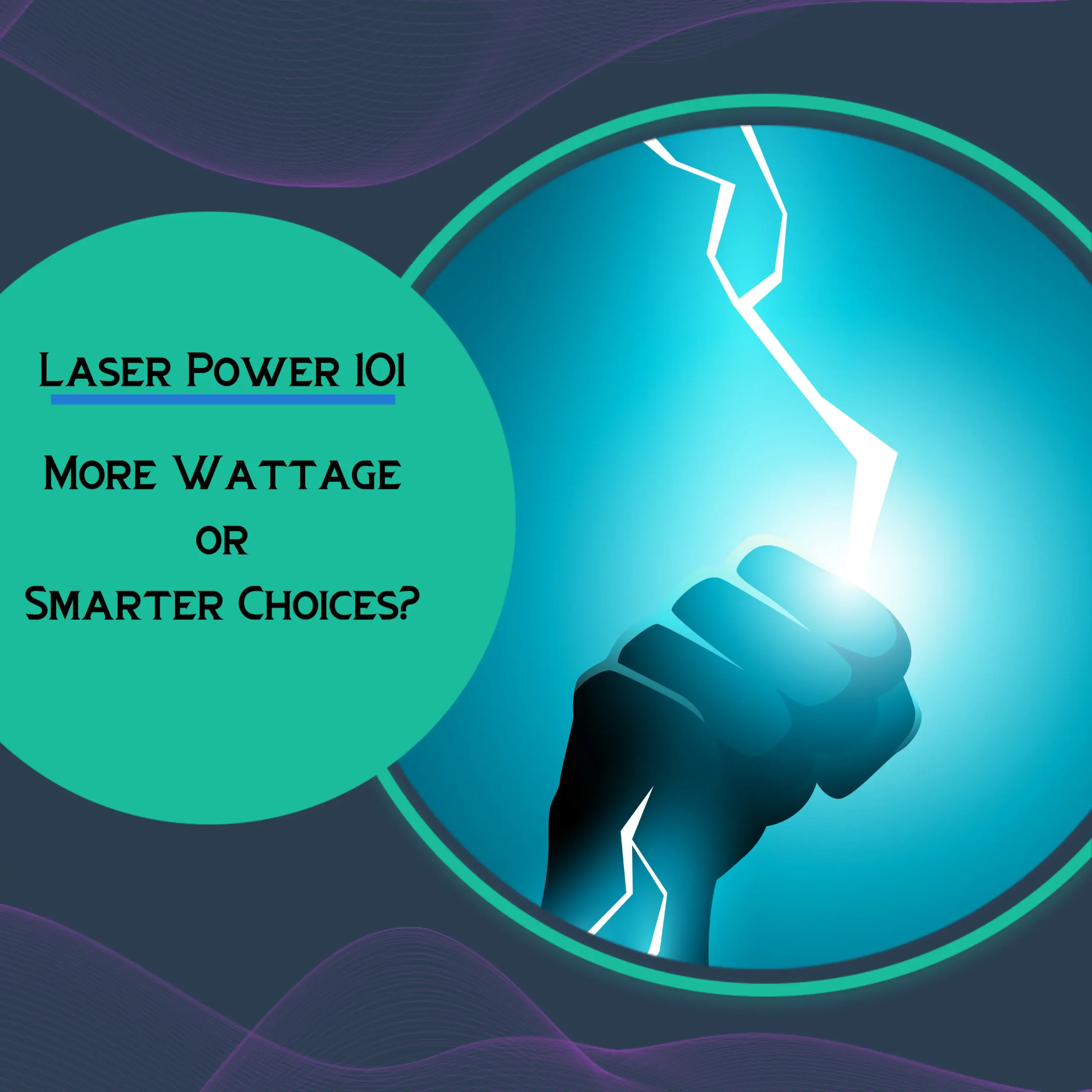
When it comes to laser technology, many ask, “Is more wattage always better?” It’s a common misconception. Many believe higher wattage equals better performance. In reality, understanding laser wattage can feel overwhelming.
You might wonder how much power you need for your applications. Does a high-wattage laser truly deliver more value? Or can a lower-wattage option handle your tasks just as well?
In this post, we’ll uncover the truth about laser power requirements. We’ll break down whether higher wattage is a must or if lower wattage can be just as efficient. By the end, you’ll have clarity on your specific needs and the confidence to make informed choices. Let’s demystify laser wattage together!
What is Laser Wattage?
Laser wattage is a critical factor in determining the performance and effectiveness of a laser system. Measured in watts (W), it indicates the power output of the laser. Wattage directly impacts how well the laser engraves, cuts, or marks various materials. A clear understanding of wattage helps users choose the right laser for their specific projects.



Understanding Laser Wattage
Laser wattage reflects the energy emitted by the laser over a given time frame. Higher wattage equates to more energy output, which often means faster engraving or cutting and the ability to handle tougher materials. Lower wattage, on the other hand, may suffice for delicate tasks but can struggle with denser or thicker materials.
Key Technical Aspects
Power Output
Laser power output is categorized by wattage. For example, the Monport Onyx 55W CO2 laser emits 55 joules of energy per second, making it ideal for most small to medium projects. In comparison, the Monport Effi16S 150W CO2 Laser Engraver delivers 150 joules per second, allowing it to handle thicker materials and large-scale tasks with ease.
Intensity
As wattage increases, the intensity and energy of the laser beam also increase, enabling it to cut deeper and process materials more quickly. However, this heightened intensity can lead to a broader laser focus point, which reduces the ability to achieve fine details in engraving. For intricate or delicate designs, lower wattage offers better precision by maintaining a tighter, more controlled laser focus. While it may require multiple passes to achieve depth, lower wattage excels in preserving detail and avoiding overburn, making it ideal for projects where accuracy and intricacy are paramount.
Engraving vs. Cutting
Engraving: Engraving typically benefits from lower wattage due to the precision it provides. Lower wattage allows for finer control over the laser’s intensity, which is essential for creating intricate details and avoiding overburn or charring on delicate materials like wood, leather, or acrylic. The reduced energy output ensures the laser doesn’t penetrate too deeply, preserving the surface’s integrity and enhancing design clarity.
Cutting: Cutting thicker or denser materials requires higher wattage. Increased power enables the laser to generate enough energy to penetrate through materials like acrylic, wood, or metal in fewer passes. This ensures cleaner edges and reduces processing time. The higher intensity of the laser beam also helps to maintain cutting efficiency on robust materials, which would otherwise be difficult to process with lower wattage.
Understanding the demands of your specific application is key to selecting the right wattage for optimal results.
Continuous vs. Pulsed Wattage
When it comes to laser technology, understanding the difference between continuous and pulsed wattage is essential for choosing the right system for your applications.
Continuous Wattage
Continuous wave lasers emit a steady, unbroken beam of energy, maintaining consistent power throughout operation. This makes them ideal for tasks requiring uniform heat, such as cutting and engraving softer materials like wood, acrylic, or leather.
Example: The Monport 55W CO2 Laser Engraver uses continuous laser output, excelling in smooth acrylic cuts and detailed wood engravings.
Pulsed Wattage
Pulsed lasers operate in bursts, delivering high peak-power outputs for very short durations. These bursts allow for greater intensity without overheating the material, making pulsed wattage especially useful for marking and engraving hard surfaces like metals.
Example: The Monport GA Series MOPA Fiber Laser Engraver features pulsed operation, making it perfect for intricate designs on stainless steel and other hard materials.
By understanding these differences, you can choose the laser system that best fits your project’s specific needs.
Practical Examples of Laser Wattage Applications
Here’s a breakdown of how laser wattage translates into real-world applications based on material type:
Material Type | Recommended Wattage | Example Laser Models |
---|---|---|
Wood (Soft, Thin) | 10W – 50W | Monport Reno 45W Pro, xTool S1 10W |
Wood (Thick) | 50W – 100W | Monport Onyx 55W, Creality Falcon2 Pro 60W |
Acrylic (Thin) | 40W – 60W | Monport Onyx 55W, xTool P2S 55W |
Acrylic (Thick) | 70W – 150W | Monport Mega 70W, Monport Effi16S 150W |
Metals (Soft) | 20W – 100W | Monport GPro 80W Split MOPA, xTool F1 Fiber Laser |
Metals (Hard) | 100W+ | Monport GPro 100W Split MOPA, Gweike CloudG6 Split MOPA 100W |
Benefits of Choosing the Right Wattage
Efficiency
Selecting the correct wattage optimizes processing times, ensuring your projects are completed faster without compromising quality. For instance, a higher wattage laser can cut through thick materials in a single pass, while lower wattage is ideal for delicate engravings, preserving fine details. This efficiency not only saves time but also reduces wear on your machine.
Precision
Higher wattage lasers excel in handling a broader range of materials with remarkable precision. Whether you’re engraving intricate designs on wood or cutting through dense acrylic, the right wattage ensures sharp, clean edges and consistent results. Precision is especially critical for professional projects where detail and quality make all the difference.
Versatility
A laser with adjustable wattage settings empowers you to take on a variety of projects, from light engraving to heavy-duty cutting. This versatility eliminates the need for multiple machines, allowing you to shift seamlessly between crafting, prototyping, and production work. Adjustable wattage also gives you better control over the outcome, tailoring the laser’s performance to the specific material and task at hand.
By understanding and choosing the right laser wattage, you’re better equipped to handle a wide range of creative and industrial projects. The right wattage not only enhances your capabilities but also ensures your laser system is a long-term, versatile tool for success.



Common Myths About Laser Wattage
When exploring the world of laser engraving and cutting, many misconceptions surround the role of wattage. Let’s uncover some of the most prevalent myths and separate fact from fiction.
Myth 1: Higher Wattage Equals Better Performance
One of the most common assumptions is that more wattage always means better results. While wattage plays a significant role in laser performance, it’s not the sole determinant of success. The choice between high and low wattage depends on your specific needs and the materials you’re working with.
Higher wattage offers the advantage of speed and power, making it ideal for tasks like cutting through thick materials or engraving large designs quickly. For example, a 100W laser can handle dense wood or thick acrylic much faster than a lower-powered system, while also achieving deeper cuts in a single pass. This makes high wattage the preferred choice for production environments or projects where time efficiency is critical.
On the other hand, lower wattage excels in precision and control, particularly for intricate designs or delicate materials. A lower-powered laser is less likely to overburn or damage materials like leather, thin wood, or paper. It allows for finer details by maintaining a smaller focus point and more controlled energy output, which is crucial for applications requiring high accuracy and subtlety.
Ultimately, the choice between higher and lower wattage comes down to the balance between speed, depth, and detail. Understanding the strengths and limitations of each will help you choose the right wattage for your specific projects.
Myth 2: Wattage Is the Only Factor for Success
Another common misconception is that wattage alone dictates the quality of a laser project. In reality, several factors work together to influence the final outcome, and understanding these nuances is essential for success.
Material properties play a significant role in determining how laser energy is absorbed. Organic materials like wood and leather readily absorb laser energy, making them easier to process with a range of wattages. In contrast, reflective or dense materials such as metals and glass require adjustments to settings like speed and frequency to achieve optimal results. Knowing how your material interacts with laser energy can help you choose the right wattage and settings.
The thickness of the material is another crucial factor. Thicker materials often demand higher wattage to ensure efficient cutting and to reduce the number of passes required. However, thinner materials can benefit from lower wattage to avoid issues like charring, warping, or excessive melting.
The intended application also influences the choice of wattage. Tasks like cutting through materials quickly and efficiently favor higher wattage for power and speed. Conversely, detailed engraving benefits from the precision and control offered by lower wattage, which minimizes the risk of overburn and allows for intricate designs.
By considering material type, thickness, and application, you can make more informed decisions about laser wattage and settings to achieve the best results for your projects.
Myth 3: All Materials Require High Wattage for Lasering
Not every material requires high wattage to deliver excellent results. In fact, many projects can achieve better outcomes with lower-powered lasers, depending on the material and the desired finish.
Softer materials such as leather, paper, and fabric often respond exceptionally well to lower wattage. Using less power allows for greater precision and minimizes the risk of issues like burning, warping, or over-penetration. This makes lower-powered lasers ideal for delicate or detailed work where control is key.
In contrast, high wattage becomes essential when working with dense or thick materials like acrylic or metal. These materials require more energy to penetrate effectively, making higher-powered lasers a better choice for cutting through robust surfaces or achieving deep engravings.
Understanding the needs of your specific materials helps ensure optimal laser performance, whether you’re prioritizing precision or power.
Myth 4: More Wattage Means More Options
While higher wattage machines offer versatility and the ability to tackle a wider range of tasks, they don’t guarantee perfect results for every material or application.
High wattage systems require skill and careful adjustments to avoid common issues like overheating or overprocessing, which can damage certain materials. Precision in setting speed, power, and frequency becomes critical to harness the full potential of higher wattage without compromising quality.
For lightweight or heat-sensitive materials like thin plastics, lower wattage often provides better results. These settings minimize the risk of warping, melting, or other heat-related distortions, allowing for clean cuts and detailed engravings without damaging the material.
Selecting the appropriate wattage for your material and application ensures both efficiency and quality, regardless of the power available in your machine.
Conclusion
Understanding laser wattage myths and realities helps users make smarter decisions. Wattage is important, but factors like material type, thickness, and application goals play an equally vital role. By combining the right machine, settings, and technique, you’ll achieve exceptional results every time.
Factors to Consider When Choosing Laser Wattage
Selecting the right wattage for your laser depends on the unique requirements of your project. Different applications demand varying power levels, and materials respond differently to laser energy. Understanding these factors ensures you make an informed choice tailored to your specific needs. Let’s explore the key considerations that influence wattage selection.
Material Properties
Density and Thickness
The density and thickness of a material dictate how it absorbs laser energy and the power needed for effective processing.
- Wood: Softer woods like pine are easier to cut and often require 20–40W. Denser hardwoods like oak or maple need 40–60W for clean, precise cuts without charring.
- Acrylic: Thin acrylic sheets (up to 1/4 inch) can be processed efficiently with 30W. Thicker sheets (1/2 inch or more) demand 60W or higher for smooth and accurate results.
Properly matching wattage to the material ensures efficiency and precision.
Color and Coating
The color and surface coating of a material influence how it interacts with laser light.
- Dark Colors: Dark surfaces, like black anodized aluminum, absorb laser energy more effectively, producing cleaner engravings.
- Light Colors or Reflective Coatings: Reflective or lighter materials, such as silver or uncoated aluminum, often require slower speeds or higher power to achieve similar results.
Adjusting settings for color and coating helps achieve consistent, high-quality outcomes.
Project Size
The size of your project impacts the wattage needed to balance speed and quality.
- Larger Projects: High wattage enables faster processing across large work areas, saving time without sacrificing precision.
- Smaller Projects: Lower wattage is better suited for detailed work, where slower speeds allow for greater control and accuracy.
Choosing wattage based on project size optimizes both workflow and results.
Desired Finish Quality
Finish quality is directly affected by laser wattage, with different levels of power offering distinct benefits.
- Higher Wattage: Ideal for professional-grade work, it allows for faster speeds and produces clean edges with intricate detail.
- Lower Wattage: Suitable for small-scale or delicate tasks, delivering excellent results with a more controlled approach.
Balancing speed and detail ensures a polished final product.
Custom Applications
Unique projects often require specific wattage to achieve the best results.
- Customized Awards: Crystal engraving typically needs 50–100W to create smooth, polished finishes without cracks.
- Intricate Jewelry Design: Small engravings on wood or soft metals benefit from 30W for precision and fine detail.
Tailoring your wattage to the application maximizes your laser’s versatility and performance.
Takeaway Tips
- Evaluate Material Properties: Consider the thickness and density of the material to determine the appropriate power needed for clean cuts and precise engravings.
- Match Wattage to Project Size: Larger projects may require higher wattage for efficiency, while smaller, detailed work often benefits from lower wattage for accuracy.
- Define Desired Finish Quality: Decide on the level of detail and edge quality you want to achieve, as this will influence your wattage selection.
- Experiment for Optimal Results: Test different wattages to explore varied effects and find the perfect balance for your specific materials and applications.
Understanding the Balance Between Power and Performance
In conclusion, while it might seem like higher wattage always guarantees better laser performance, this isn’t the full picture. The effectiveness of a laser depends on several factors, such as the material type, the precision and speed needed, and the specific applications you have in mind. While higher wattage can enable faster processing, it doesn’t necessarily lead to better results for every scenario.
Before committing to a specific wattage, take the time to evaluate your unique needs. Consider how different wattages interact with the materials you plan to use and match them to your project requirements. By finding the right balance of power and efficiency, you’ll maximize your laser’s potential while staying within budget.
Let’s Stay Connected!
Dive deeper into laser engraving and cutting by exploring our material tests and project ideas:
- 🌟 Follow Us on YouTube: ADT Studios YouTube Channel
- 🌟 Connect with Us on Facebook: ADT Studios Facebook Page
- 🌟 Explore Material Tests: Material Tests
- 🌟 Discover Inspiring Projects: Creative Projects
Stay inspired and informed! Follow us on social media for tips, tutorials, and project showcases. Don’t forget to like, comment, and subscribe to our YouTube channel for the latest updates. Let’s create something amazing together! 😊
This is super helpful! Thanks for shedding light on laser power requirements.
I used to just think more wattage meant faster cuts, but now I see it’s more complicated!
Does anyone know if there are specific tasks where high wattage is actually necessary?
Love how you broke it down! Makes it clear that more isn’t always better.
Interesting points! I guess it’s all about finding the right balance.
Great article! I’ve always wondered if higher wattage really means better results.