Stitch Density Simplified: A Beginner’s Guide to Fabric Customization
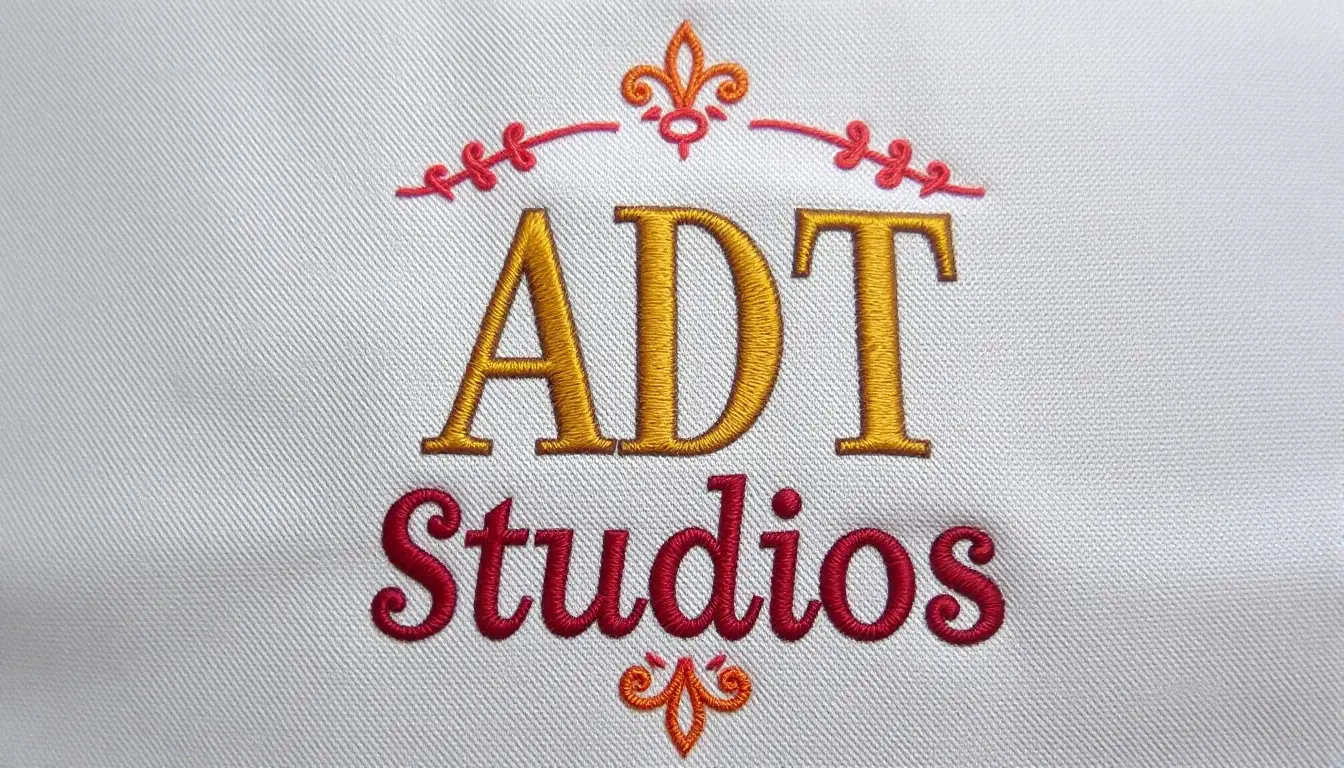
Achieving the perfect stitch density is crucial for creating professional-quality embroidery designs. This comprehensive guide takes you step by step through determining the right stitch density for different fabrics. Matching stitch density to the fabric type is essential for ensuring your designs are not only visually appealing but also durable. By exploring the relationship between stitch density and fabric characteristics, you’ll gain the skills to enhance texture, appearance, and longevity in your embroidery projects. Let’s dive into the details and unlock the secrets to flawless stitching!

Understanding Stitch Density
Stitch density, defined as the number of stitches per inch (SPI) in your embroidery design, plays a critical role in achieving the desired look and feel of your project. Higher stitch densities create a denser, more textured appearance, ideal for bold designs or intricate details. In contrast, lower stitch densities result in a softer, more fluid aesthetic, often better suited for lightweight or delicate fabrics.
To truly master stitch density, it’s essential to experiment. Test different densities on sample fabrics to observe how they influence both the texture and visual appeal of your designs. Keep in mind that your choice of fabric and thread significantly affects the outcome. Thicker fabrics may handle higher stitch densities well, while thinner materials might require reduced density to prevent puckering or distortion.
By understanding these principles and practicing with various combinations, you’ll gain the confidence to customize stitch density to suit any fabric or design, elevating the quality of your embroidery projects.



Identify Your Fabric Type:
To determine the ideal stitch density, start by identifying your fabric type. Focus on the fabric’s texture and stretch rather than its weight. Feel the material to assess whether it’s smooth like silk, coarse like burlap, or soft like cotton. Stretch the fabric gently to determine its elasticity, as stretchier fabrics often require specific stitch adjustments to maintain stability.
Observe the fabric’s drape by holding it up and letting it fall naturally. This step helps you anticipate how the material will behave during and after stitching. Some fabrics, such as knits, may require stabilizers to prevent distortion, while others, like tightly woven cotton, offer more stability on their own.
Understanding these characteristics allows you to adjust your stitch density for better results. For example, smoother fabrics benefit from tighter, precise stitching to avoid slippage, while textured materials may need looser stitches to achieve even coverage. Always consider the unique properties of your fabric when planning your embroidery design.
By thoroughly analyzing your fabric type, you can tailor your stitch density to complement its unique qualities, ensuring your embroidery designs maintain both aesthetic appeal and structural integrity.
Fabric Weight
Fabric weight significantly impacts how stitch density should be adjusted for optimal embroidery results. Pairing the right density with the fabric’s weight ensures a polished design that maintains the material’s integrity.
- Heavier Fabrics: For materials like denim, wool, or canvas, use a higher stitch density. These robust fabrics can support dense stitching, enhancing detail and creating a durable design.
- Lighter Fabrics: For delicate fabrics such as silk, chiffon, or lightweight cotton, choose a lower stitch density. This reduces strain on the fabric and prevents issues like puckering or distortion.
Aligning stitch density to fabric weight ensures the design sits naturally on the material, delivering a flawless finish while preserving the fabric’s strength and appearance.
Test Different Stitch Densities
Testing stitch densities is a critical step in refining your embroidery projects. By experimenting with varying densities, you can discover the perfect balance for your chosen fabric and design.
- Why Testing Matters: Testing reveals how stitch density affects the look, texture, and durability of your design on a specific fabric.
- Steps to Test: Create multiple small swatches with the same design but adjust the stitch density for each. Label the samples with their respective density settings to track the outcomes.
- What to Observe: Pay attention to how well the stitches cover the fabric, whether puckering occurs, and how durable the embroidery feels. Also, notice any color changes caused by overlapping threads.
Testing helps you avoid guesswork, giving you confidence that your final project will look polished and professional.
Consider Thread Type
Thread type significantly influences how your stitch density interacts with the fabric. Choosing the right thread ensures a smooth embroidery process and a flawless result.
- Thread Thickness: Thicker threads, such as metallic or upholstery threads, demand lower stitch densities. Using fewer stitches allows the thread to sit naturally on the fabric without creating bulk.
- Finer Threads: Embroidery threads, such as rayon or polyester, perform best with higher stitch densities. Closer stitches enhance coverage and produce intricate details.
- Color Impact: The type of thread can affect how colors blend or layer. Thicker threads may overpower details, while finer threads can provide subtle gradients.
Adjust your stitch density to accommodate your thread’s characteristics, ensuring compatibility with your design and fabric.
Factor in Design Complexity
Complex designs require careful consideration of stitch density to maintain clarity and balance. Whether you’re working on intricate patterns or simple shapes, tailoring density settings is essential.
- Intricate Designs: For designs with small text, fine details, or tight patterns, use a higher density. This ensures each element is clearly defined and doesn’t lose its shape.
- Simple or Large Designs: For larger, open designs, reduce density to avoid overworking the fabric and to create a lighter, more breathable finish.
- Visual Harmony: Balance stitch density across the design. Combining areas of high density with low-density sections can add depth and texture, making your project visually appealing.
By tailoring density to the design’s complexity, you ensure that every detail stands out without compromising the overall look.
Check for Fabric Stretch
Stretchy fabrics, such as knits or spandex, present unique challenges when determining stitch density. Proper adjustments can prevent distortion and maintain the fabric’s integrity.
- Lower Density for Stretch: For fabrics with significant stretch, opt for a lower stitch density. This allows the material to flex without pulling or puckering the stitches.
- Targeted Coverage: If more coverage is necessary, slightly increase the density in specific areas. However, be cautious not to exceed the fabric’s stretch capacity.
- Stabilizer Importance: Use a stabilizer designed for stretchy fabrics to minimize movement during stitching. This ensures a smooth and professional finish.
Adapting stitch density for stretch fabrics ensures your embroidery remains durable and visually appealing while preserving the fabric’s flexibility.
Analyze Stitch Type
Different stitch types interact uniquely with fabrics and require tailored densities to achieve the best results. Understanding these differences can elevate your embroidery projects.
- Satin Stitches: Best suited for smooth, non-textured fabrics. Lower density creates a sleek, polished look without overburdening the fabric.
- Fill Stitches: Ideal for thicker or textured materials. Higher densities provide complete coverage, ensuring even color and texture.
- Running Stitches: Use minimal density for outlines and delicate details. This avoids fabric stress and maintains a clean, lightweight appearance.
Consider how each stitch type complements your design and fabric. Adjusting density to match the stitch style ensures a harmonious and durable final product.
Review Manufacturer Recommendations
Fabric and thread manufacturers often provide detailed guidelines to help you determine optimal stitch densities. Leveraging this information can save time and improve results.
- Fabric Recommendations: Look for specific density suggestions tailored to the material’s composition and intended use. This can prevent common issues like puckering or distortion.
- Thread Guidance: Many thread brands specify densities suited for their products. These recommendations ensure smooth operation and vibrant, consistent results.
- Use as a Starting Point: While manufacturer guidelines are helpful, don’t hesitate to adjust them based on your design and fabric. Testing remains essential for fine-tuning.
Consulting these resources helps you make informed decisions and achieve consistent, high-quality results in your embroidery projects.
Document Your Stitch Density Findings
Creating a log of your successful stitch densities and settings ensures future projects are efficient and consistent.
- Organized Records: Maintain a notebook or digital file where you document fabric type, thread used, stitch density, and design specifics.
- Visual Samples: Include photos of your completed projects alongside notes to provide a clear reference.
- Build a Resource Library: Over time, your documentation will become a valuable resource for troubleshooting and planning new projects.
Recording your findings eliminates guesswork and streamlines your creative process, enabling you to focus on perfecting your craft.
Key Takeaways and Tips
Mastering stitch density unlocks the full potential of your embroidery projects. By tailoring density to fabric, thread, and design, you achieve stunning, professional-quality results. Remember, each project is a learning opportunity—experiment, document, and refine your techniques to continually enhance your skills. Happy stitching!
For more tips, tutorials, and inspiration, follow us on YouTube and connect with us on Facebook. Don’t forget to explore our projects page to see how we apply these techniques and discover new creative ideas! Let’s create something amazing together!
Essential Equipment List


Mastering Stitch Density for Flawless Embroidery
Visually assessing stitch density is a crucial step in ensuring your embroidery designs turn out as planned. Here’s a refined approach to evaluating whether your stitch density is appropriate:
- Print a Sample Design
Begin by printing a sample of your design at its intended size. This provides a realistic preview of how the stitch density will appear on the finished product. - Examine Your Fabric
Evaluate the fabric you plan to use. Different fabrics respond uniquely to stitch density due to their texture, weight, and weave. Ensure the density enhances the fabric’s natural characteristics without overpowering or distorting it. - Check for Gaps or Overcrowding
Inspect the stitched area for uniform coverage. Too few stitches may leave noticeable gaps, while excessive density can result in clumping, puckering, or distortion of the fabric. - Test in Various Lighting Conditions
Examine your design under different lighting conditions. Bright, natural light or focused task lighting will help reveal inconsistencies or flaws that might not be obvious under dimmer lighting. - Use Magnification Tools
If necessary, use a magnifying glass or loop to closely inspect the details of your stitches. This ensures even spacing and proper coverage, especially in intricate or detailed areas. - Evaluate Based on Design Intent
Consider the purpose of your design. Densely stitched areas are ideal for detailed elements, while simpler or larger sections may benefit from a lighter, more spaced-out stitch density.
By systematically following these steps, you can confidently determine whether the stitch density in your designs aligns with your aesthetic goals and practical requirements. Taking the time to evaluate this detail ensures a polished, professional-quality result in every project.
Does anyone have a preference for stitch types on thicker fabrics? Would love some input!
Wow, I never realized stitch density could make such a big difference. Mind blown! 🤯
Why didn’t I think of this sooner? This is a game changer! 💡
Anyone else struggle with stretch fabrics? Could use more advice on that!
Great tips! I can’t wait to try out different densities on my next project. 🧵✨
Just learned about the basting stitch! Didn’t know it could help with density. So cool!
I always thought it was just me messing up! This really clarifies a lot. Thanks!
Thanks for sharing this! I’m definitely going to experiment with my next sewing project.
This is super helpful! I always had issues with my lightweight fabrics.
Loved this article! Finally understand why my stitches are different on various fabrics! 😍